Leading Die Casting Parts Manufacturers: Your Guide to High-Quality Metal Fabrication
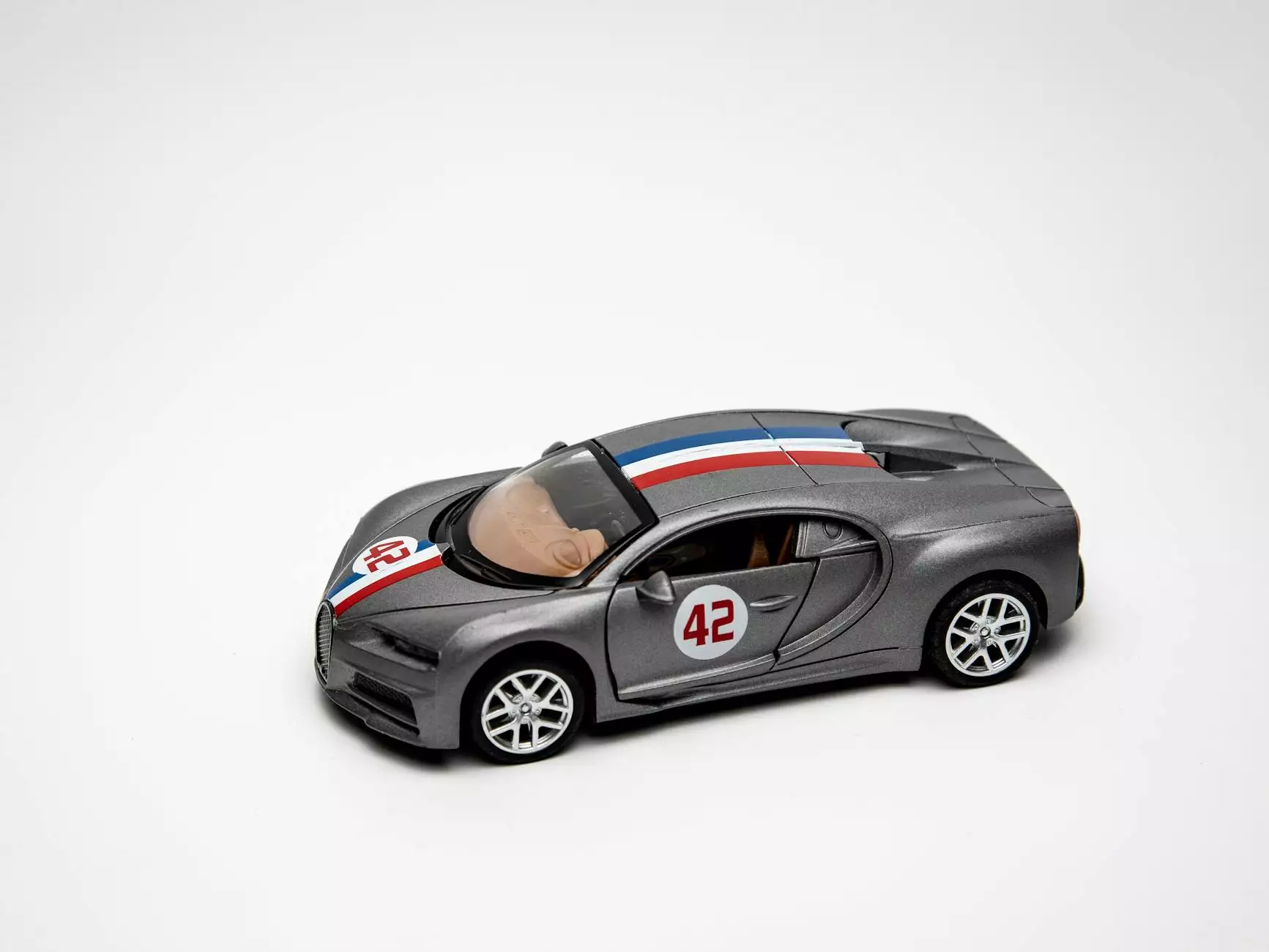
Understanding Die Casting
Die casting is a metal fabrication process that utilizes pressure to force molten metal into a mold cavity. This method is widely acclaimed for its production efficiency and the ability to create complex shapes with high accuracy. The die casting process is particularly advantageous due to its capability to produce parts with exact dimensions and smooth finishes, resulting in minimal post-processing needs.
The Role of Die Casting Parts Manufacturers
Die casting parts manufacturers play a crucial role in numerous industries, supplying high-quality components tailored to specific applications. Factors such as precision, strength, and surface quality are paramount, and these manufacturers focus on delivering products that meet or exceed industry standards.
Benefits of Partnering with a Die Casting Parts Manufacturer
Choosing to work with a reputable die casting parts manufacturer offers several notable advantages, including:
- Cost Efficiency: Dies can be reused multiple times, significantly reducing production costs per part over time.
- High Precision: The die casting process ensures that parts are produced with high dimensional accuracy.
- Complex Geometries: Manufacturers can create intricate designs that would be difficult or impossible with traditional machining processes.
- Material Versatility: A broad range of materials can be used, including zinc, aluminum, and magnesium alloys.
- Reduced Waste: The process generates less scrap material compared to other metalworking techniques.
Core Industries Utilizing Die Casting Parts
Die casting parts are integral to various sectors, notably:
- Automotive: Engine blocks, transmission cases, and other critical components.
- Aerospace: Lightweight and high-strength parts for aircraft and spacecraft.
- Consumer Electronics: Enclosures, housings, and brackets that deliver durability.
- Medical Devices: Precise components for equipment that demand strict regulatory adherence.
- Construction: Architectural features, fittings, and fixtures that require robust performance.
Key Processes in Die Casting
The die casting process involves several critical steps, each essential for producing quality parts:
- Preparation of the Mold: The mold design is finalized, ensuring it can withstand the pressure of molten metal.
- Heating: The die is heated to reduce thermal shock and help the molten metal flow into the mold easily.
- Pouring Molten Metal: The molten metal is carefully poured or injected into the pressurized mold cavity.
- Cooling: The metal cools and solidifies quickly, maintaining the shape of the mold.
- Mold Opening and Part Ejection: Once cooled, the mold is opened, and the parts are ejected.
- Finishing: Additional processes such as sanding, polishing, or coating can be applied to achieve the desired finish.
Quality Assurance in Die Casting
Quality assurance is a fundamental aspect of die casting parts manufacturing. Manufacturers typically implement rigorous testing processes, including:
- Dimensional Inspection: Ensuring parts meet specified tolerances.
- Material Testing: Analysis of metal properties to confirm thermal and mechanical characteristics.
- Surface Quality Assessment: Checking for defects in finish and texture.
- Functionality Testing: Ensuring the components perform as intended in real-world applications.
Environmental Considerations in Die Casting
As industries evolve, the focus on environmental sustainability has grown. Die casting parts manufacturers are adopting more sustainable practices to reduce their ecological impact:
- Recycling Scrap Metal: Many manufacturers recycle scrap materials generated during the die casting process.
- Energy Efficiency: Updating equipment to utilize less energy during production.
- Low-Emission Solutions: Implementing cleaner technologies in metal melting and handling.
- Waste Management: Developing policies to minimize waste and manage byproducts responsibly.
The Future of Die Casting Parts Manufacturers
As technology advances, die casting parts manufacturers are poised for significant evolution. Innovations such as:
- Automation: Automation in die casting processes will increase efficiency and reduce labor costs.
- 3D Printing Technology: Combining traditional die casting with 3D printing for rapid prototyping and new design possibilities.
- Industry 4.0: Integrating smart sensors and data analytics in production lines for improved quality control.
- Advanced Alloys: Development of new alloys that enhance performance and reduce weight.
Choosing the Right Die Casting Parts Manufacturer
Selecting a die casting parts manufacturer is a crucial step for any business. Here are essential factors to consider:
- Experience: Look for manufacturers with a proven track record in your industry.
- Capacity: Ensure they have the capacity to handle your production needs.
- Technology: Evaluate their use of advanced technology to ensure high-quality production.
- Customer Support: Strong communication and support are vital for a successful partnership.
- Certifications: Check for ISO certifications and other relevant industry standards.
Conclusion
In conclusion, die casting parts manufacturers are pivotal in providing high-quality, durable components across a plethora of industries. Their expertise in metal fabrication, commitment to quality, and drive towards sustainability make them indispensable partners. By understanding the die casting process and the key characteristics of reputable manufacturers, businesses can make informed choices that contribute not only to their success but also to the advancement of the manufacturing industry as a whole.