Plastic Injection Tooling Made in China: A Comprehensive Guide
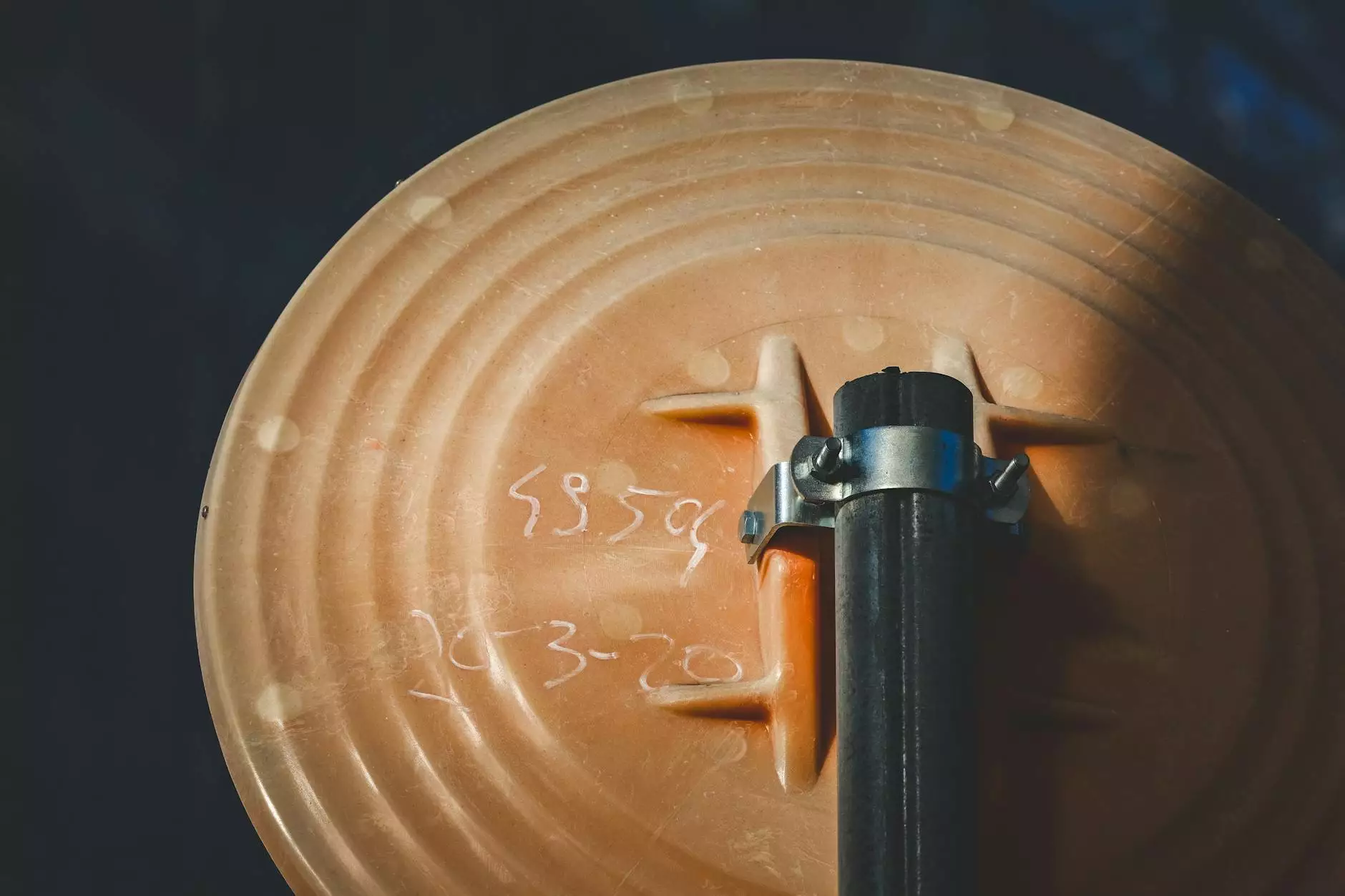
In the world of manufacturing, plastic injection tooling made in China has become a significant player, revolutionizing how companies create and produce a vast range of plastic products. From automotive components to toys, the applications are limitless. This article delves into the nuances of this industry, providing insights into why Chinese manufacturers are at the forefront of innovation in plastic injection tooling.
What is Plastic Injection Tooling?
Plastic injection tooling refers to the process of creating a mold, which is then used for manufacturing various plastic parts. The tooling process is crucial, as it determines the precision, quality, and overall cost of the final product. Over the years, the demand for high-quality, cost-effective solutions has surged, and China has emerged as a global leader in this field.
The Plastic Injection Molding Process
The plastic injection molding process involves several steps:
- Design and Engineering: It begins with designing the required part using CAD software. Detailed specifications are created to ensure accuracy.
- Tool Manufacturing: Tools are crafted based on the design. This phase is critical as mistakes in the mold can lead to production failures.
- Injection: Once the tooling is in place, plastic pellets are heated until they melt and are injected into the mold under high pressure.
- Cooling: The injected plastic cools inside the mold, solidifying into the final shape.
- Demolding: The cooled product is removed from the mold, completing the cycle.
The Advantages of Plastic Injection Tooling Made in China
China has positioned itself as a powerhouse in plastic injection tooling due to several advantages:
Cost-Effectiveness
One of the most compelling reasons for choosing plastic injection tooling made in China is the cost savings it offers. Labor and material costs are relatively low, enabling manufacturers to offer competitive prices while maintaining quality standards.
Advanced Technology and Expertise
Chinese manufacturers are increasingly investing in advanced technologies and skilled labor. This investment ensures that they can produce high-quality tooling that meets international standards. Companies like Deep Mould exemplify this commitment, employing state-of-the-art machinery and techniques to deliver superior products.
Rapid Turnaround Times
Time is often of the essence in production. Chinese companies are recognized for their ability to deliver products quickly, making them ideal partners for businesses that require fast production cycles. Efficient logistics and a well-established supply chain further enhance their capabilities.
Applications of Plastic Injection Tooling
The versatility of plastic injection molding means it is used in various industries:
- Automotive: Manufacturing durable interior and exterior components.
- Consumer Electronics: Creating casings for smartphones, tablets, and other devices.
- Medical Devices: Producing precise parts that adhere to stringent regulations.
- Toys: Crafting colorful and complex shapes that attract children.
- Household Goods: Making everyday items such as storage containers and kitchen tools.
Quality Control in Plastic Injection Tooling
Quality control is paramount in any manufacturing process. In plastic injection tooling made in China, several measures are implemented to ensure that the final products meet the required standards:
Material Selection
The selection of high-quality materials is essential. Many Chinese manufacturers use advanced plastics and comply with international regulations, ensuring safety and durability.
Inspection Processes
Regular inspections are conducted throughout the production process. This includes:
- Visual checks of molds for any flaws.
- Testing samples for dimensional accuracy.
- Stress testing to evaluate the durability of the final product.
Certifications
Many manufacturers obtain international certifications, such as ISO and CE markings, providing assurance of their commitment to quality and compliance with global standards.
Sustainability and Eco-Friendly Practices
As the world becomes increasingly aware of environmental issues, manufacturers are striving to implement sustainable practices in plastic injection molding. Chinese companies are no exception:
Recycling Initiatives
Many manufacturers have begun to embrace recycling initiatives, using recycled plastics in their processes. This move not only minimizes waste but also reduces production costs.
Energy Efficiency
Investments in energy-efficient machinery and renewable energy sources are becoming commonplace. This commitment to sustainability can significantly reduce the environmental impact of manufacturing operations.
The Future of Plastic Injection Tooling in China
The future of plastic injection tooling made in China appears bright, with several trends shaping the industry:
Automation and Smart Manufacturing
As technology advances, the integration of automation in manufacturing processes will increase productivity and efficiency. Smart factories equipped with IoT (Internet of Things) technology allow for real-time monitoring and adjustments, enhancing quality control and reducing downtime.
Growth in Emerging Markets
With a vast array of products manufactured using plastic injection molds, demand will continue to grow in emerging markets. China is positioned to cater to this increased demand with its scalable production capabilities.
Choosing the Right Manufacturing Partner
When you're looking for plastic injection tooling made in China, selecting the right manufacturing partner is critical. Here are some factors to consider:
Experience and Reputation
Evaluate the manufacturer's track record. Consider companies with years of experience and positive client testimonials, such as Deep Mould.
Technical Capabilities
Ensure that the manufacturer utilizes advanced machinery and has a skilled workforce capable of meeting your specific needs.
Communication and Support
Effective communication is vital for a successful partnership. Choose a supplier that offers excellent customer service and can respond to your needs promptly.
Certifications and Compliance
Verify that potential partners possess the necessary certifications to ensure that their processes meet international quality and safety standards.
Conclusion
In conclusion, the realm of plastic injection tooling made in China is not only vast but also encompasses numerous benefits, applications, and future opportunities. The combination of cost-effectiveness, technological advancements, and a commitment to quality ensures that China will continue to be a dominant player in this sector. By understanding the intricacies of this industry, businesses can make informed decisions and establish fruitful partnerships that drive innovation and growth.
As the demand for high-quality plastic products continues to soar, so does the importance of choosing the right tooling methods and manufacturers. Engage with reputable companies, such as Deep Mould, to explore how they can help you navigate this dynamic landscape and achieve success in your manufacturing endeavors.